Centrifuge Shear Prediction
Client Profile
A major global Phosphate and Potash mining company faced challenges with their centrifuge operations, also known as “Big Birds.”
The Challenge
- Frequent unexpected shears causing 20-30 minutes of downtime per shear
- Operators setting shear setpoint high or using bypass option to avoid shearing
- Both options leading to damage of Bird motor / Rotor assembly
- Need for real-time shear predictions to minimize downtime and equipment damage
Process Point's Solution: Data-Driven Intelligence
Data Collection and Analysis
- Comprehensive data gathering from multiple sources
- Advanced data cleaning and preprocessing
- In-depth data analysis to uncover insights
Advanced Modeling and Machine Learning
- Development of sophisticated models
- Machine learning algorithms for predictive analytics
- Continuous model training and optimization
AI/ML Predictive Maintenance Model
- Predictive maintenance to reduce downtime
- Real-time anomaly detection
- Proactive maintenance scheduling
Real-Time Monitoring and Automation
- Continuous monitoring of operations
- Automated control systems
- Immediate response to operational changes
Results and Benefits
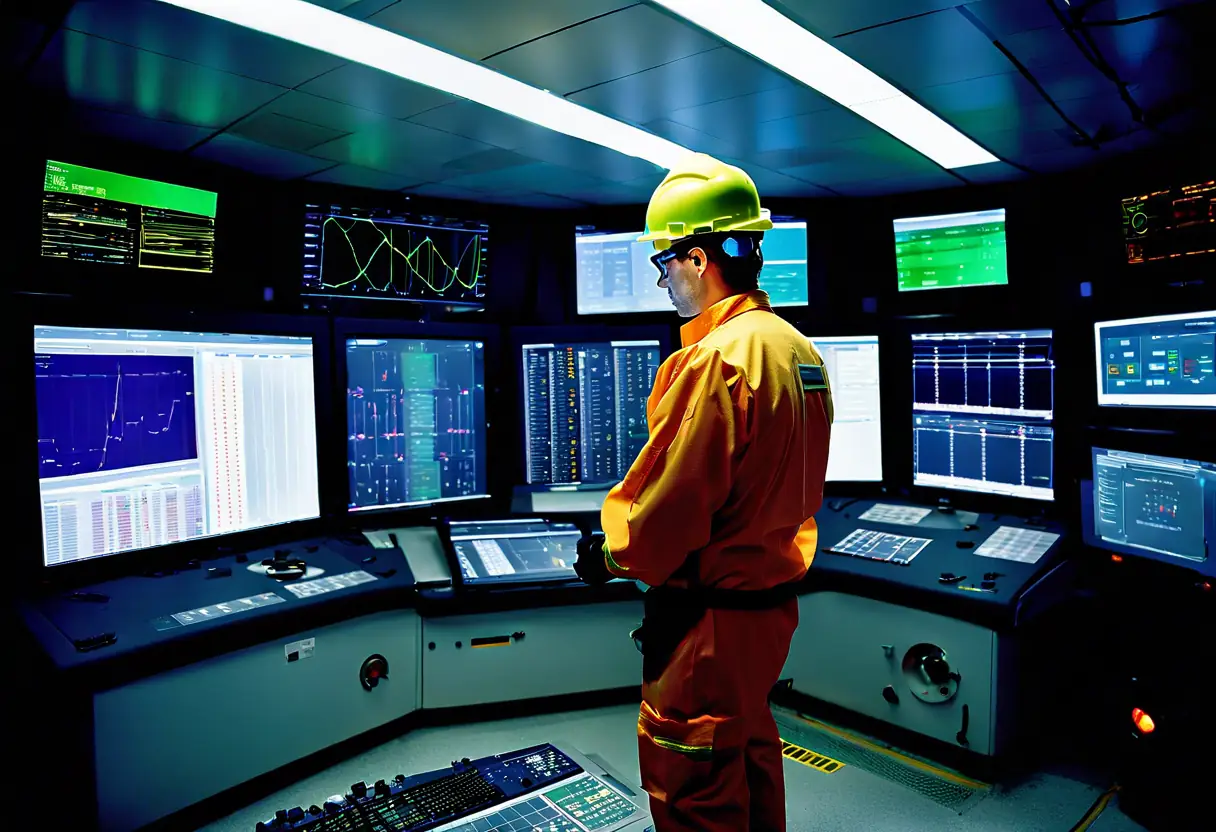
Real-Time Predictions
Accurate real-time predictions of centrifuge shears allow for proactive maintenance, preventing unexpected issues.
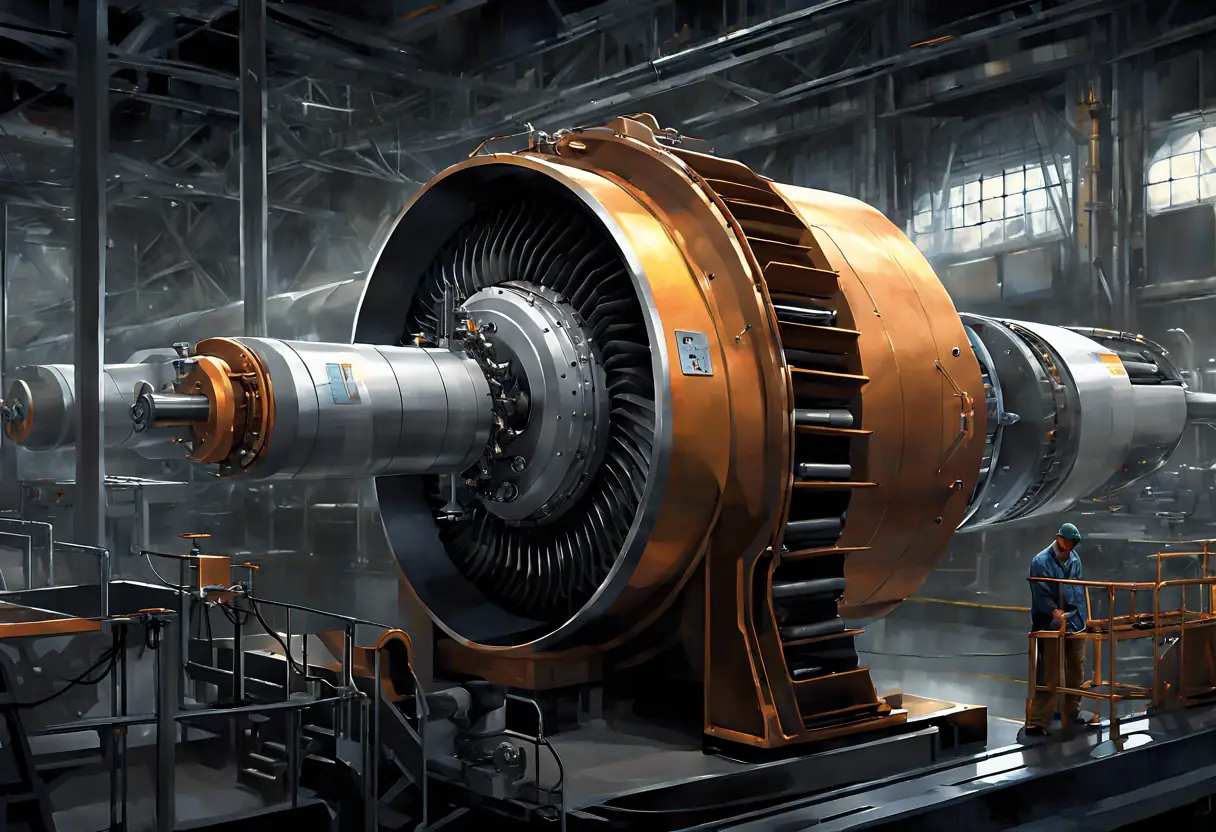
Reduced Downtime
Significant reduction in unexpected downtime, previously 20-30 minutes per shear, thanks to our predictive maintenance approach.
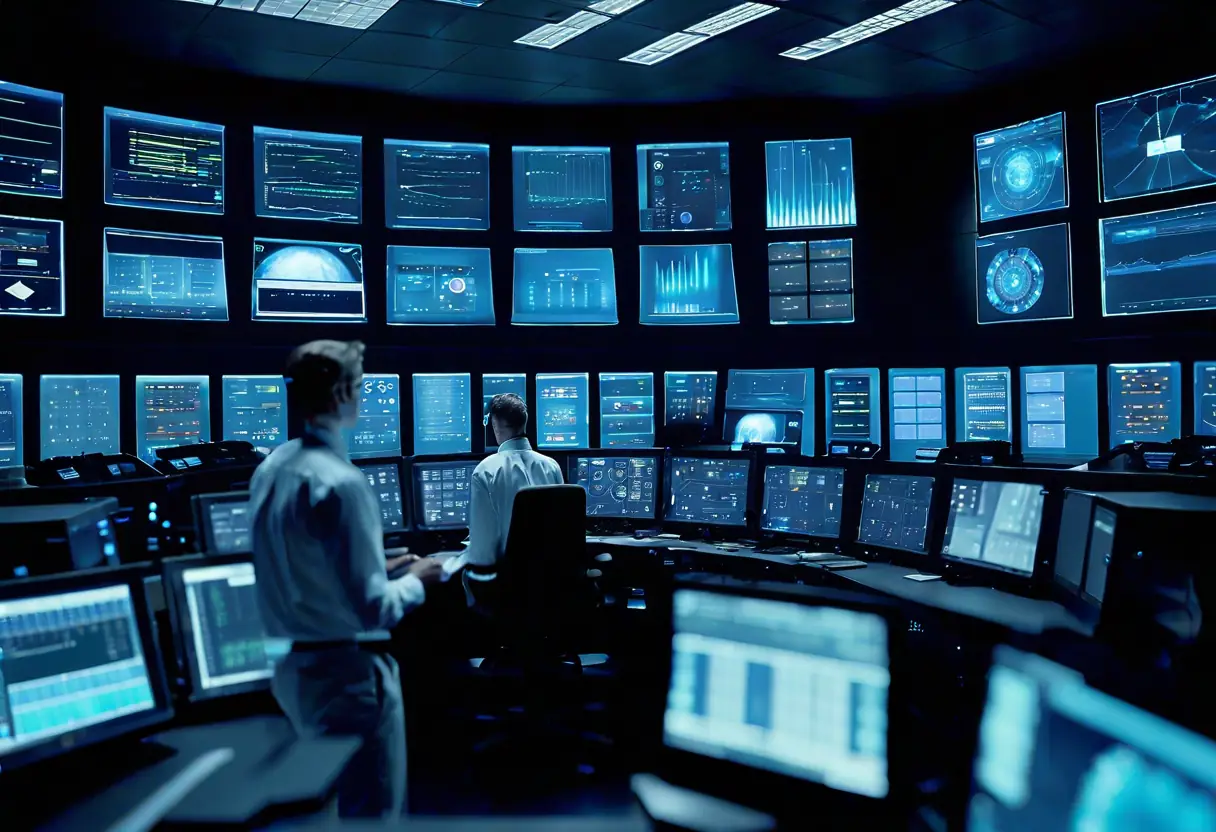
Empowered Operators
Operators are empowered with data-driven insights, enabling them to make informed decisions for optimal centrifuge operation.
Conclusion
By leveraging ProcessPoint’s expertise in data-driven intelligence, the client significantly improved the efficiency and reliability of their centrifuge operations. The implementation of advanced AI/ML models for predictive maintenance led to substantial cost savings, increased productivity, and enhanced equipment longevity. This case study demonstrates the transformative power of data analytics and machine learning in solving complex industrial challenges, positioning the client at the forefront of innovation in the phosphate and potash mining industry.